Как правило, клапаны проходят заводские испытания давлением для проверки на возможность утечки перед отправкой. Тип и метод тестирования соответствуют одному или нескольким из множества различных стандартов. Цель этих тестов и ожидаемые результаты часто неправильно понимаются и используются конечным получателем, что приводит к ненужным задержкам и непредвиденным расходам.
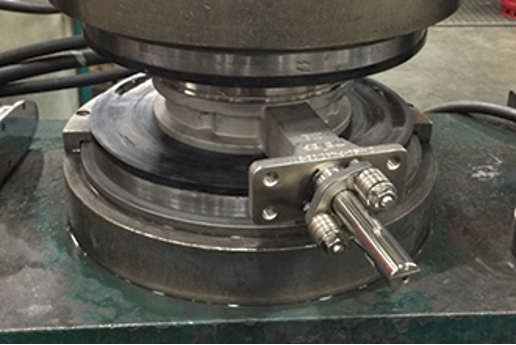
Существует множество стандартов, определяющих требования к испытаниям на герметичность кранов и клапанов. Часто разница между ними неясна, что приводит к путанице в том, какой из них использовать и почему. Для начала нужно понять, что существует два типа утечек, подвергаемых испытаниям:
- Внешняя — это утечка из-за давления внутри клапана, выходящая в атмосферу. Ее отсутствие подтверждается испытанием корпуса. Внешняя утечка не допускается при давлении равном или превышающем номинальное значение клапана.
- Внутренняя — это утечка вокруг седла клапана или через запорный элемент, когда клапан закрыт. Внутренняя утечка обычно происходит в системе трубопроводов. Такая утечка может быть также внешней, если клапан используется в конце трубопровода. Внутренняя утечка проверяется испытанием герметичности седла или испытанием на закрытие. Допустимая скорость утечки зависит от стандарта испытаний клапана.
Методы испытаний на внешние и внутренние утечки определены в многочисленных стандартах. Их слишком много, чтобы охватить в одной статье, однако, ниже мы приведем краткое пояснение некоторых наиболее распространенных стандартов:
- Американское общество инженеров-механиков (ASME) B16.34 - Клапаны фланцевые, резьбовые и под приварку: это наиболее широко используемый стандарт проектирования клапанов и кранов. Он содержит таблицы, которые определяют рабочее давление, используемое в сочетании с другими стандартами испытаний, такими как API 598. ASME B16.34 содержит методы испытаний, но не определяет допустимую утечку через седло.
- Американский институт нефти (API) 598, Проверка и испытание клапанов: это наиболее широко используемая в мире спецификация испытаний. Данный стандарт охватывает многие типы трубопроводной арматуры, но был разработан, прежде всего, для запорных типов клапанов и кранов. Он включает в себя классы герметичности и критерии испытаний для арматуры как с металлическими, так и с мягкими седлами.
- Общество по стандартизации в промышленности (MSS) SP61, Гидростатические испытания стальных клапанов: данный стандарт схож с API 598, но имеет небольшие различия во времени выдержки при испытаниях и классах герметичности. Это был один из первых стандартов испытаний трубопроводной арматуры, но он не получил широкого распространения в мире. Однако, стоит заметить, что он послужил основой для более поздних стандартов.
- Международная организация по стандартизации (ISO) 5208, Промышленные клапаны, Испытания клапанов давлением: это основной стандарт ISO по испытаниям, охватывающий многие типы клапанов. Он описывает 10 уровней допустимой внутренней утечки (классы герметичности), а также критерии приемки, подлежащие согласованию между покупателем и производителем.
- Американский национальный институт стандартов (ASNI) FCI 70-2, Утечка в седле регулирующего клапана: в этом стандарте подробно описаны процедуры испытаний и классы герметичности для регулирующих клапанов. Классы герметичности также иногда упоминаются в других документах и используются в качестве критериев приемки. Стандарт имеет шесть различных уровней герметичности от Класса I до Класса VI. Здесь важно отметить, что ANSI FCI 70-2 предназначен только для внутреннего тестирования. Он не применим для тестирования внешней герметичности клапана и отсылает пользователей к API-598 для тестирования запорной арматуры.
- Международное общество автоматизации (ISA) S75, Гидростатические испытания регулирующих клапанов: этот стандарт описывает процедуру внешнего тестирования регулирующих клапанов. Испытания на закрытие и критерии приемки выходят за рамки этого документа и обычно охватываются ссылкой на ANSI FCI 70-2.
ИСПЫТАНИЕ КОРПУСА КЛАПАНА НА ПРОЧНОСТЬ
Обычно первой остановкой в производственном процессе уже собранного клапана является внешний тест, известный как испытание корпуса гидростатическим давлением. Этот тест подтверждает надежность и прочность корпуса клапана. Он также предварительно опрессовывает корпус клапана, что помогает избежать быстрого износа от циклического давления. В целях безопасности это испытание обычно проводится с водой, давление которой в полтора раза превышает номинальное давление корпуса клапана. Подобное испытание также обычно проводится на полностью собранном клапане в частично открытом положении.
Для испытаний корпуса стандарт API-598 ссылается на ASME B16.34, в котором представлены значения номинального давления корпуса, в зависимости от материала. Например, клапан класса 150 из углеродистой стали (например, WCB) испытывается при давлении 31 бар. Тот же клапан из нержавеющей стали (например, CF8M) испытывается при давлении 29 бар. Стандарты EN (Европейский комитет по стандартизации) и DIN (Немецкий институт стандартизации) учитывают только номинальное давление корпуса. Так, вне зависимости от материала корпуса, клапан PN10 испытывается при давлении в 15 бар, а PN40 - при 60 бар. Клиенты, ведущие международный бизнес и привыкшие работать со стандартами EN и DIN, нередко заявляют, что было применено неправильное испытательное давление при испытании корпуса клапана в соответствии с API или ASME.
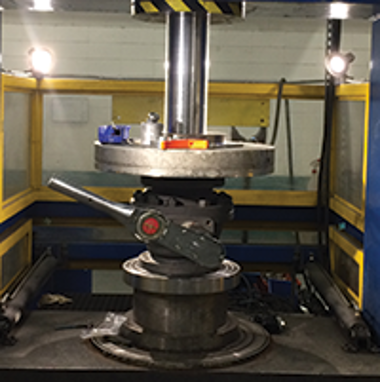
Кроме того, даже такой простой тест, как испытание корпуса на прочность, имеет следующие проблемы:
- Чувствительность: в некоторых случаях отливки корпуса клапана имеют пористость, крайне маленькую для того, чтобы вода могла просачиваться сквозь них, что обычно называется микропористостью. Чаще всего это происходит в отливках из монеля и бронзы. Чтобы обнаружить дефект в таком типе литья, сначала необходимо проверить клапан воздухом, а затем погрузить его в воду или покрыть снаружи мыльным раствором. Такая пористость может быть заблокирована, и в этом случае она не будет обнаружена, если клапан сначала нагнетается под давлением воды, поскольку воды достаточно, чтобы заблокировать путь утечки. В стандартах клапанов не упоминается об этом дополнительном испытании, но целесообразно использовать такие испытания с литыми материалами с повышенным риском, предназначенными для работы с опасными и смертоносными газами.
- Сила зажима: клапаны с разъемным корпусом обычно зажимаются в гидравлическом прессе для герметизации концов при испытании под давлением. Если не контролировать процесс должным образом, сила зажима может легко превысить дозволенную нагрузку на соединительную прокладку корпуса, создаваемую болтовым соединением корпуса. Когда это происходит, соединительная прокладка может быть чрезмерно сжата, что приведет к ослаблению болтов и, возможно, к внешней утечке.
- Специальные чистые клапаны: Клапаны, используемые в таких средах, как кислород, хлор и перекись водорода, требуют дополнительной очистки и проверки, чтобы гарантировать их безопасное использование. Вода внутри полностью собранного клапана может привести к нежелательным и небезопасным загрязнениям, а любая остаточная вода, появившаяся после испытания, может быть опасна при установке в эксплуатацию. Например, остаточная вода, остающаяся в клапанах для криогенной эксплуатации, может замерзнуть и помешать работе клапана. В таких случаях лучше всего проверить корпус перед сборкой клапана.
- Коррозия: Остаточная вода внутри клапанов и кранов из углеродистой стали может привести к щелевой коррозии, особенно агрессивному типу коррозии, которая может повредить критические уплотнительные поверхности и привести как к внутренней, так и к внешней потере герметичности. Попытки удалить воду путем запекания или нагрева клапана при повышенных температурах, как правило, неэффективны.
- Содержание хлоридов: опасения по поводу коррозионного растрескивания нержавеющей стали привели к ограничению содержания хлоридов в испытательной воде, определенному в нескольких стандартах. Как правило, предел составляет около 50 миллионной доли (ppm), а некоторые стандарты доходят до 30 ppm или ниже. Особенно трудно достичь низкого стабильного уровня хлоридов, если на предприятии используется общественная или городская система водоснабжения.
- Безопасность: рассмотрев проблемы тестирования водой в специальных чистых клапанах, а также риска коррозии, возникает соблазн полагать, что тестирование воздухом является лучшим выбором. Иногда это правда. Однако, поскольку воздух сжимаем, объем воздуха, который сжимается в испытательном клапане, может быть очень опасным, если что-то лопнет, и энергия внезапно высвободится. Согласно Руководству по неразрушающему контролю Американского общества неразрушающего контроля, воздействие относительно небольшой ударной волны давления воздуха может привести к следующим травмам:
Таблица 1. Избыточное давление ударной волны
> 5 psi (0.34 бар) |
Разрыв барабанной перепонки |
> 15 psi (1 бар) |
Необратимое повреждение легких |
> 35 psi (2.4 бар) |
Смертельные случаи |
- Сервисный ремонт: возникает вопрос, нужно ли после ремонта клапана повторять испытание корпуса. Если исходная оболочка, работающая под давлением, не была изменена во время технического обслуживания, нет необходимости повторять испытание, так как прочность корпуса клапана останется неизменной, ведь испытания уже были проверены в ходе первоначальной заводской проверки. Однако, если произошла сильная коррозия или был проведен ремонт сварных швов, необходимо повторить испытание корпуса.
ВНУТРЕННЕЕ ТЕСТИРОВАНИЕ
Хотя аргументы относительно вопросов внешней герметичности или тестирования корпуса кажутся значительными, они менее сложны, чем вопрос внутренней герметичности. Что касается внутренней герметичности, необходимо понимать, что такие термины, как нулевая утечка и герметичность, часто неправильно интерпретируются, что является очень распространенной грубой ошибкой. Выражения «герметичность» и «нулевая утечка» требуют дальнейшего изучения. Таблица 2 определяет измеримые скорости утечки и объясняет их в повседневных терминах.
Таблица 2.
Скорость утечки |
Эталонная скорость утечки |
Описание |
1 х 10 -8 |
1 см3 в каждые 3 года |
Диффузия гелия через стекло на квадратный сантиметр площади поверхности. |
1 х 10 -7 |
3 см3 в год |
Размер 3х шариков или игральной кости. |
1 х 10 -6 |
1 см3 в каждые 2 года |
Дыхание на утечку такого размера может обеспечить достаточно влаги, чтобы временно закрыть утечку на несколько часов. |
1 х 10 -5 |
1 см3 в день |
Смачивающее средство или мыло необходимо добавить в воду, предназначенную для тестирования, чтобы визуально определить утечку такого размера. |
1 х 10 -4 |
1 см3 в каждые 3 часа |
Можно визуально определить поднимающиеся пузырьки в воде. |
1 х 10 -3 |
4 см3 в час |
Утечка такого размера легко обнаруживается в воде при кратковременном испытании. Это уровень чувствительности типичного заводского испытания воздухом. |
1 х 10 -2 |
Слишком много! |
Слышен звук от утечки. |
Большинство испытаний на внутреннюю герметичность клапана проводится с воздухом в течение относительно короткого периода времени, от нескольких секунд до нескольких минут. Этого времени достаточно, чтобы обеспечить быстрое визуальное наблюдение за значительной утечкой, не будучи чрезмерно затратным по времени и не снижая возможности завода по изготовлению и отгрузке клапанов.
Хоть поднимающиеся пузырьки в воде можно наблюдать уже и со скоростью утечки 1 x 10-4 см3 в секунду, заводские испытания непродолжительны, поэтому чувствительность типичных заводских испытаний на герметичность составляет около 1 x 10-3 см3 в секунду. Это примерно эквивалентно четырем кубам (четыре игровых кубика или шарика) утечки в час. Как правило, подобная утечка незначительна, потому что газу потребуются годы, чтобы просто заполнить объем трубы после клапана.
Увеличение продолжительности с нескольких минут до часа приводит к тому, что чувствительность теста достигает диапазона 1 x 10-4 см3 в секунду. Это эквивалентно одному игровому кубику или шарику по объему утечки за три часа.
Часто неопытный техник наносит мыльный раствор на закрывающий элемент и ждет час или более, прежде чем наблюдать образование пены. Этот метод тестирования обеспечивает уровень чувствительности 1 x 10-5, что эквивалентно одному игровому кубику или шарику утечки за один день. Принимая во внимание некоторые из опасных газов, которые может содержать клапан, разумно надеяться, что соединения корпуса и другие статические уплотнения в клапане будут герметичными при испытании с использованием этого метода. Однако, не следует ожидать, что запорные элементы, которые являются динамическими уплотнениями, будут обеспечивать такой уровень герметичности.
Существует множество различных типов клапанов и типов конструкции затвора с различными материалами. Отсюда существует и множество стандартов тестирования, учитывающих уникальное поведение каждого из них.
ПРИЧИНЫ
Неспособность прочитать и понять причины, лежащие в основе методов испытаний, приводит ко второй наиболее распространенной ошибке, заключающейся в убеждении, что заводские испытания проводятся для подтверждения того, что клапан будет работать при номинальном давлении. Стандарты API и ISO тщательно определяют риск такого мышления. Каждый из них содержит важное примечание, предупреждающее о том, что испытания клапанов с мягким седлом под высоким давлением могут ухудшить работу при низком давлении. Настоящая цель заводского испытания на внутреннюю герметичность - проверить качество конечного продукта, а не прочности конструкции. Испытание на внутреннюю герметичность должно соответствовать типу клапана, и это должно быть самым сложным и комплексным испытанием клапана. Клапаны с эластичным седлом могут иметь уплотнения, работающие под давлением, в этом случае более высокое давление может увеличить силы уплотнения, потенциально маскируя любые дефекты размеров или поверхности. Для таких типов клапанов сложнее пройти испытание низким давлением, и это лучший показатель качества сборки.
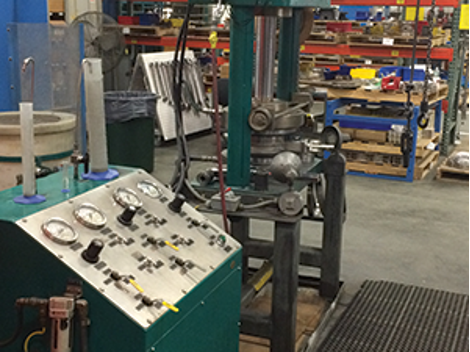
Для запорной арматуры, работающей в двухпозиционном режиме, подходят стандарты ASME, API и ISO. Они также могут быть применимы для регулирующих клапанов, которые должны обеспечивать изоляцию в процессе эксплуатации. Например, дисковые затворы поворотные часто используются как для регулирования, так и для изоляции. Если стандартное заводское испытание основано на API или ISO, нет необходимости проводить дополнительное испытание согласно ANSI FCI 70-2, поскольку качество сборки клапана уже было проверено.
НА ПРОИЗВОДСТВЕ
Третья распространенная ошибка состоит в заблуждении, что заводские производственные испытания показывают, как клапан будет работать в эксплуатации. Часто конечные пользователи указывают, что клапан должен быть испытан при расчетном давлении и температуре технологического процесса. Хоть это и не проблема лаборатории, оборудованной для проведения подобных испытаний, это непрактично делать в типичной заводской среде. Такие испытания являются подтверждением конструкции клапана, а не качества сборки.
Жизнь была бы проще, если бы все клапаны были ограничены отсутствием утечек на время испытания. Но это технически невозможно. Для испытания клапана давлением целесообразно использовать стандартную практику, применяемую производителем. Производитель не хочет отправлять дефектный продукт и, естественно, мотивирован использовать самые требовательные методы испытаний с наименьшим риском повреждения клапана.
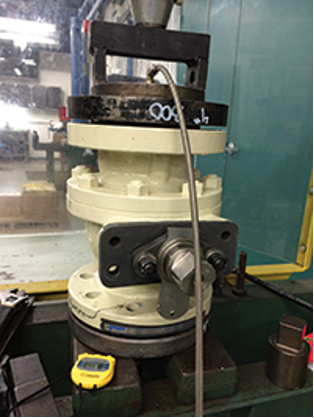